造桥、造火箭,3D打印真的无所不能?
本文来自微信公众号:Nature自然科研(ID:Nature-Research),原文作者:Mark Zastrow,题图来自:视觉中国
一个金属平台从一片液态树脂中升起来,随之出现了一个精致的白色模型——就像一个光滑的生物从一片泻湖中逐渐现身。
这是世界上最快的树脂3D打印机,它可以在几小时内打印出与人体尺寸相当的结构。这台高速树脂3D打印机由美国西北大学的化学家Chad Mirkin及其同事研发,并在去年十月报到了这一研究成果[1],这是3D打印领域的重大突破,拓宽了这一原本只能制造小型低精度原型零件的技术的应用范围。
3D打印技术不仅变得更快、打印尺寸更大,同时科学家们还提出一系列创造性的技术改进手段,研发出强度更高的材料,甚至在单一产品上混合了多种材料进行打印。
Chad MirKin位于美国西北大学的实验室中有一台树脂打印机,它可以在几小时内制造出与人体尺寸相当的结构。图片来源:西北大学。
运动服装厂、航空航天制造商和医疗器械公司都十分渴望有效利用3D打印的优势。哈佛大学的材料科学家Jennifer Lewis说:“虽然短期内我们还不能在家里快速打印出修理汽车所需的零件,但这一技术已被主流制造公司采用。”
这项最新技术也有望给研究人员带来经济收益,像 Lewis 和 Mirkin一样,他们中的很多人已经开始对自己的成果进行商业化的尝试。英国谢菲尔德大学的冶金学家Iain Todd表示:“3D打印技术的进步可以让我们通过超乎想象的方式来利用这些材料,这让材料科学家们十分兴奋,也将让人们逐渐习惯于3D打印的全新事物。”
从零件到产品
3D打印技术也被称为增材制造,与从整块的原料切削和磨削制造或从利用熔融金属和模具进行铸造的传统工艺流程不同,3D打印是一种自底向上的制造过程。它具有较低的材料消耗和高度的定制化能力,能够制造像网格这样传统方法难以制造的复杂结构。
业余爱好者使用的低成本机器通过将塑料成份的原料线源源不断送入加热后的喷嘴中,随后喷嘴将融化后的塑料不断挤出,一层接一层地向上构建设计的结构,这也被称为熔融沉积成型工艺(fused deposition modelling,FDM)。
但3D打印所涵盖的技术远远不止于此,最早的方法之一就是利用紫外激光对光敏树脂进行逐层扫面固化,这一概念可以追溯到1984年Chars Hu[2]的专利,他同时也是美国南卡罗来纳州3D Systems公司的创始人。
最新的3D打印技术,包括Mirkin的技术在内,仍然在使用光敏树脂,但随着北卡罗来纳大学教堂山分校的化学家、材料科学家Joseph DeSimone领导的团队在2015年报告出改进方法后[3],3D打印的速度和尺寸都有了大幅提升。
早期的3D打印机速度较慢,打印的尺寸较小,并且容易产生分层、有瑕疵的脆弱结构。这种打印技术只能有限地应用于快速原型设计,为基于传统方法的正式生产制造塑料模型。作为研究领域来说,这种打印技术还无法令研究人员满意,澳大利亚墨尔本莫纳什大学的高分子科学家Timothy Scott表示:“用这种方法只能制造一些小零件和小玩意儿,那对于一个高分子化学家来说十分无趣。”
2015年,北卡罗来纳大学教堂山分校的Joseph DeSimone提出了一种可以加速3D打印的技术。图片来源:Carbon 3D Inc
DeSimone随后发现了一种可以将光敏树脂打印速度相较于传统打印机提升100倍的新途径[3]。这种方法将工作台浸没于树脂容器中,随后用投影仪将预先编程过的图像通过容器底部的透明窗口照射到工作台上。
这种方法可以让光一次性固化整层树脂。该方法的优势在于底部的窗口可以透过氧气,这会阻止固化反应并在窗口上方产生一层很薄的缓冲层(也称为死区),让每次打印出的树脂层不会粘附在容器底部。随着工作台不断地上升,新层不断打印出来,已完成的部分则被不断拉出液态树脂。
Lewis表示还有很多其他实验室利用相似的概念进行研发,但DeSimone的方法令人印象深刻的一点在于,它可以在打印后利用热处理来实现第二种反应,增加成品的强度。Lewis说:“这为3D打印打开了更广阔的材料空间。”
此后很多研究团队和公司都在此基础上进行更深入的研究。Mirkin的打印机选择将一层清油泵到容器的底部以阻止高分子反应。同时这层油还起到了冷却剂的作用,将带走打印过程中产生的热,防止打印出的部件变形。这也意味着这种打印机不仅仅可以打印厌氧的树脂。
Mirkin表示,他的打印机比DeSimone的设备又得到了十倍的速度提升。去年一月在密歇根大学安娜堡分校,Scott和 Mark Burns提出了一种新的方法来抑制反应,通过向树脂中混合一种可以被另一束不同波长的光源激活的化学物质来实现[4]。通过调节两种光强的比例,研究人员可以控制光抑制区域的厚度,使得更为复杂的模式打印成为可能,例如带有图印或者标志的表面结构。
3D打印领域的创新具有迅速商业化的潜力,一些研究人员在发表论文之前就开始着手建立公司了。例如在发表论文当日,DeSimone在温哥华发表TED演讲时就宣布在加州雷德伍德城建立一家名为Carbon 3D的初创公司。
实际上他在两年前就已经悄悄注册了这家公司,如今它已经成为3D打印领域最大的初创公司之一,目前已募集了6.8亿美元,估值达到了24亿美元。它与Adidas高调签订合约,为运动鞋生产类似橡胶的鞋底夹层,同时与运动装备公司Riddell签订了为美式足球运动员生产头盔衬里的合同。
Carbon 3D的技术被用于打印Adidas的鞋底(左侧)和美式橄榄球头盔的衬里(右)。图像来源:Carbon 3D Inc.
Mirkin和同事James Hedrick及David Walker也在伊利诺伊的埃文斯顿创立了一家名为“Azul 3D”的初创公司,将他们的高区域快速打印(high-area rapid printing,HARP)技术商业化。Scott 和 Burns也在为他们位于安娜堡的初创公司Diplodocal准备商业化原型打印机,值得一提的是,他们公司的名字Diplodocal来源于“双光束”的希腊语。
新的树脂打印技术还在涌现,其中一种技术将液态树脂装入了旋转的玻璃管中,随着玻璃管的旋转,投影仪将一段视频投射到玻璃管中,而视频则对应着目标形状的2D切片,只用几秒钟的时间,需要打印的物体就会在玻璃管中固化,这样就不再需要一层层地堆叠打印了[5]。
这种方法受到了X射线和计算断层扫描技术的启发,它们通过横截面来为物体成像。而这种打印方法则反过来将横截面图像反投影回去,以形成3D目标。
一架投影仪将视频循环投射入液态树脂中,使得整个物体可以一次成型而无需一层接一层地堆叠。图片来源:加州大学伯克利分校
即使在这一飞速发展的领域,这项引人注目的技术也被Lewis称为绝妙的想法。不过,这种方法有很大的局限:需要树脂足够透明,并且目标物体不能太大,否则光线无法穿过树脂,无法固化。但这种技术显示出了潜在的优势,它可以处理非常粘稠的树脂,因为其他树脂打印机在狭窄的“死区”中难以进行抽取。这意味着这种方法可以构建强度更高,精度更高的结构。
劳伦斯·利弗莫尔国家实验室的材料和制造工程师Christopher Spadaccini表示,这种方法已经吸引了工业界的广泛兴趣。Spadaccini也是去年一月发表了这项技术的团队的一员[5]。而瑞士洛桑联邦理工学院也独立地提出了类似的概念,并提前几个月将成果发布在了预印本服务器上[6]。Spadaccini认为这一技术具有巨大的商业价值,因为其硬件要求十分简单,“最终,你只需要一台一般的投影仪和一个转台就可以了。”
规模变大
当化学家们致力于研究更为智能的3D方法来打印复杂的树脂构件,工程师们则不断拓展着3D混凝土打印的边界——利用计算机和机器人来精确地自动化浇筑过程。
一座由清华大学建造的3D打印混凝土行人桥梁。图片来源: Imaginechina/Shutterstock
世界上第一座3D打印的混凝土行人桥梁,由西班牙巴塞罗那的加泰罗尼亚先进建筑研究所的研究人员设计建造,并于2016年安装在了马德里附近阿尔科文达斯的一座公园里。这座桥长12m,外形呈现出网格状结构,这是由算法优化后以最大化强度和最小化金属用量的处理结果。清华大学的工程师在上海也建造了一座类似的26m长的桥梁。另外,来自中国和荷兰公司的团队也建造了3D打印的样板房。
然而这些建筑并不是由一个整体的打印件构成,而是通过多个打印好的部件拼接而成。通过更为便宜和高效的方式建造桥梁和房屋,3D打印可以减少混凝土的碳排放,但是也会鼓励工程师建造更多。
并不只有混凝土才能打印大型构件,来自阿姆斯特丹的MX3D公司就利用不锈钢打印了一座桥,它于2018年首次公开展示,目前安装了一系列传感器进行测试,之后计划安装到阿姆斯特丹的一条运河上。
MX3D的打印机正在打印金属桥梁。来源:Olivier de Gruijter/MX3D
洛杉矶的初创公司Relativity Space正在建造几乎全部由3D打印制造的火箭,其目标是将1250 kg的物资送入低地轨道,计划于2021年进行首次发射测试。Relativity Space的CEO Tim Ellis表示,打印的金属可能并不总是具有传统方法所制金属构件的散热性能,但3D打印可以增加一系列传统制造方法无法生产的几何构型的制冷通道。同时,火箭几乎是一次性或者只用几次的用品,所以长期来看,火箭的结构无需像飞机的合金一样坚固、耐受数万次的压力循环。
初创公司Relativity Space的金属打印机——计划于2021年测试一个主要利用3D打印技术制造的火箭。图片来源:Relativity Space
这些大规模的金属打印项目利用机械臂将金属丝送入到激光熔融区域来构建物体。其他成熟的3D金属打印方法还利用激光或电子束,将金属粉末融化来打印产品。还有一种方法利用胶水将金属粉末粘合,而后送入熔炉中烧结成型。最近几年还出现了与FDM类似的方法,将熔融金属从喷嘴中挤出来进行打印。
像波音、劳斯莱斯、普拉特·惠特尼等航空公司开始使用3D打印来制造喷气式发动机的金属部件,这种方法比铣削更便宜并使得复杂构件更为轻巧。
但3D打印的金属具有一系列会降低产品强度的结构缺陷。Spadaccini等人正尝试利用传感器阵列和高速相机来观察结构中的非规则性,包括应变积累点和温度热点,并作出实时调整。
很多科学家还致力于改进打印金属构件的内在强度,例如通过控制材料的微结构来实现。2017年10月,一个美国团队报告称,利用高温和急冷的方法处理3D打印的不锈钢材料,可以改变金属的微结构,并实现了超过铸造工艺的产品强度[7]。
两个月前,美国和澳大利亚的研究团队报告了具有相似的强度优势的钛铜合金[8]。先前的3D打印方法会使得钛合金在固化时形成圆柱状的结构晶粒,而铜则可以加速固化过程,使得晶粒更小并向各个方向发展,从而增强了目标整体的结构强度。
Mark Easton是澳大利亚皇家墨尔本理工大学的一名材料工程师,也是上述合金项目的负责人之一。他已经与对这种材料的应用前景感兴趣的航空航天企业展开对话,他表示这种材料同样可以用于像人工关节之类的医疗植入物中。
很多适用于金属的打印技术也同样可以用于陶瓷,潜在应用包括制造牙冠和骨科植入物。它们的模具目前已经开始利用3D打印制造,而后利用传统的铸造手段来制造。但利用3D打印整个产品,可以大大节省看牙和看外科的时间。
伦敦帝国理工学院的材料与陶瓷科学家Eduardo Saiz表示,目前还较难控制3D打印陶瓷中的微结构,几乎所有的陶瓷打印技术都涉及大量的烧结后处理,这会造成部件的变形或翘曲,“依我看,陶瓷的实际应用将落后于聚合物与金属。”他说。
不断发展的打印技术
这一领域的未来方向被称为“4D打印”,其中3D打印的物体会具有一定的机械运动能力——类似人造肌肉。这种技术通常会结合形状记忆聚合物,这些材料会在环境温度和湿度改变的情况下作出反应。
2018年5月,苏黎世联邦理工学院和加州理工学院的研究人员打印出了一种水下装置,当被置于温水中时,它可以利用向后弹起的桨来推动自身向前运动[9]。这有望催生出一种能够自主探测海洋的微型机器人,但目前需要在每次划水后重置桨叶。
澳大利亚伍伦贡大学的材料工程师Geoff Spinks认为,可以利用电池驱动桨叶重置,但这会使得机器人的效率甚至低于传统的驱动方式。“4D打印仍然存在一系列重大的挑战。”他说。
另一类4D打印方法引入了变化的外部磁场来触发动作。美国的研究人员构建了一种内部填充液体且液体可随磁场变硬的3D打印栅格状结构[10],这种技术也许能在未来被应用于汽车座椅,使其在受到撞击时变硬。
一种响应磁场变硬的液体被注入到中空结构和3D打印的栅格状结构中,这种材料可以实现刚性和柔性的转换。图像来源:Julie Mancini/LLNL
此外,4D打印更为被动的潜在应用还包括血管支架,它可以被压缩植入到血管中,当到达目标位置时将拓展展开结构。去年七月,来自瑞士和意大利的研究人员研究了一种宽度仅为50微米的4D打印支架[11]。这种比传统支架小很多的结构,有望在未来被用于治疗类似于尿道狭窄等有可能危及胎儿生命的疾病。
也许关于4D打印最为雄心勃勃的例子,要数那些不但会动而且确确实实有生命的应用了。目前,类似于可以进行皮肤一类组织打印的生物打印技术已经适用于实验室研究,同时也可以为已成功植入大鼠的肝脏和其他器官进行组织修补。研究人员梦想有一天可以打印出完整功能的器官,从而减少器官移植的等待时间。“但这一技术还远未达到可以应用于人体的水平,至少还需要十几年的时间。”Lewis说。
您目前设备暂不支持播放
集大成者
Scott表示,很多关于打印材料的创新性想法依赖于多种材料的同时打印,“那绝对是3D打印领域的前沿方向。”
去年十一月,Lewis及其实验室描述了一种可以迅速切换或混合不同高分子打印材料的打印机[12],这意味着它可以打印出既具有刚性部分又具有柔性部分的物体。Lewis依靠先前在多材料打印机方面的工作,在马塞诸塞州的萨默维尔创立了一家名为Voxel8的公司。
她说这种多材料打印机可以有效改善目前Voxel8的运动装置开发。可穿戴设备需要在关节附近保持灵活,但同时也需要具备容纳电子设备的刚性部分。Saiz称赞这种打印机是一项“美丽的作品”,还若有所指地补充了一句:“它和打印陶瓷或金属的设备截然不同。”
佐治亚理工学院的材料工程师Jerry Qi带领一支团队,在2018年三月推出了四合一的3D打印机:一个喷嘴可以挤出熔融聚合物,一个可以打印光敏树脂,输出的光敏树脂可以通过紫外灯或者激光进行固化;另外两个则可以利用微小金属点打印导线和电路[13]。
通过打印头之间的协同工作,可以将电路嵌入到刚性基板或柔性高分子外壳内,集成制造出所需的设备。Qi表示团队目前正在与电子行业的公司合作,他们对于这种比传统方法更加快速的电路板原型打印技术十分感兴趣。
这不是简单地将四种不同的打印机整合在一起,研究人员还需要开发出能够使得打印头互相通信并追踪打印过程的软件系统。
这一领域目前还远未实现将制造带入千家万户的早期愿景。就目前而言,复杂精密的打印机价格高昂,阻碍了非专业人士的购买和使用,但3D打印在过去的20年里已经走过了很长的发展道路。
Todd还记得在2000年前后人们参观他的实验室,看到将金属粉末融合制成零部件的技术时的情景。与隔壁的铣刀机床和切割系统相比,他的3D打印机器深深地吸引了参观者。他回忆道:“参观者们看到这项技术时,就像看到了狗狗在酒吧中弹钢琴一样惊讶!”但现在这项技术已经成了很多工厂的标配了。
参考文献:
1. Walker, D. A., Hedrick, J. L. & Mirkin, C. A. Science 366, 360–364 (2019).
2. Hull, C. W. Apparatus for production of three-dimensional objects by stereolithography. US patent 4575330A (1984).
3. Tumbleston, J. R. et al. Science 347, 1349–1352 (2015).
4. de Beer, M. P. et al. Sci. Adv. 5, eaau8723 (2019).
5. Kelly, B. E. et al. Science 363, 1075–1079 (2019).
6. Loterie, D., Deirot, P. & Moser, C. Preprint at ResearchGate
https://doi.org/10.13140/RG.2.2.20027.46889 (2018).
7. Wang, Y. M. et al. Nature Mater. 17, 63–71 (2018).
8. Zhang, D. et al. Nature 576, 91–95 (2019).
9. Chen, T., Bilal, O. R., Shea, K. & Daraio, C. Proc. Natl Acad.Sci. USA 115, 5698–5702 (2018).
10. Jackson, J. A. et al. Sci. Adv. 4, eaau6419 (2018).
11. deMarco,C.etal.Adv.Mater.Technol.4,1900332(2019).
12. Skylar-Scott,M.A.,Mueller,J.,Visser,C.W.&Lewis,J.A.Nature 575, 330–335 (2019).
13. Roach, J. D. et al. Add. Manuf. 29, 100819 (2019).
本文来自微信公众号:Nature自然科研(ID:Nature-Research),原文作者:Mark Zastrow
网址: 造桥、造火箭,3D打印真的无所不能? http://www.xishuta.com/newsview22598.html
推荐科技快讯
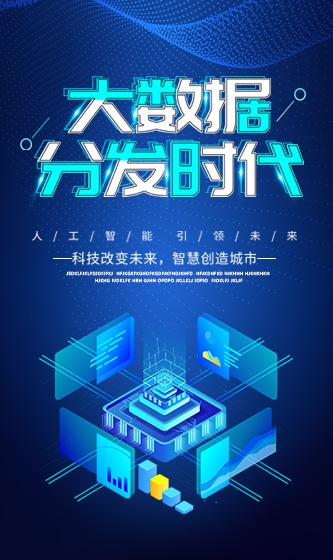
- 1问界商标转让释放信号:赛力斯 95228
- 2人类唯一的出路:变成人工智能 21183
- 3报告:抖音海外版下载量突破1 21148
- 4移动办公如何高效?谷歌研究了 20339
- 5人类唯一的出路: 变成人工智 20338
- 62023年起,银行存取款迎来 10336
- 7五一来了,大数据杀熟又想来, 8596
- 8网传比亚迪一员工泄露华为机密 8505
- 9滴滴出行被投诉价格操纵,网约 8215
- 10顶风作案?金山WPS被指套娃 7230